Rigid-flex PCBs integrate rigid PCBs and flexible circuits into one integrated interconnect solution. They enable 3D circuit routing, eliminate connectors and cables, and minimize space in electronic devices. Rigid-flex is increasingly used in consumer electronics, medical devices, automotive, aerospace, and military applications. This article explores the top 10 rigid-flex PCB manufacturers worldwide known for rigid-flex technology expertise and capabilities.
RayMing is the leading rigid-flex PCB manufacturer worldwide. With over 25 years of experience, RayMing specializes in producing complex, high-reliability rigid-flex boards for medical, automotive, industrial, and aerospace applications. Packaging Film
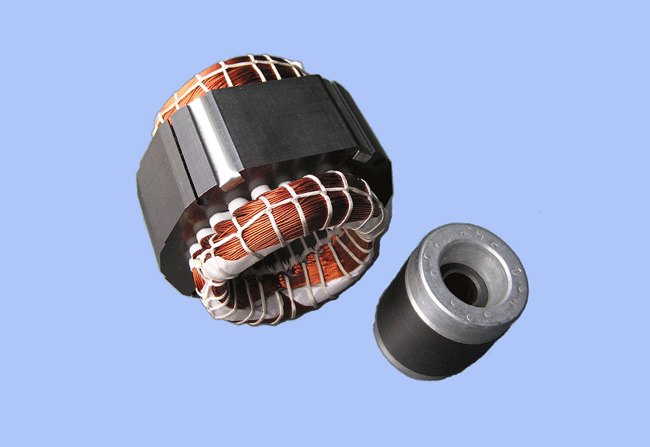
RayMing's rigid-flex capabilities include:
RayMing possesses expertise across all rigid-flex design styles including rigid islands, rigid sections, folding flexes, and complex rigid-flex combinations. They seamlessly manage the PCB fabrication through assembly for turnkey rigid-flex solutions.
Flexium is a leading flexible and rigid-flex PCB manufacturer based in Taiwan. For over 20 years, they have produced high-end flex and rigid-flex boards for consumer electronics and wearable products globally.
Flexium possesses extensive capabilities spanning:
Flexium provides advanced flex and rigid-flex technology while maintaining cost competitiveness. Their quality focus has attracted tier one electronics brands worldwide.
MFLEX, headquartered in California, provides advanced flex and rigid-flex PCBs globally. They specialize in high complexity designs meeting demanding miniaturization, high density, and high speed requirements.
With rigorous process controls and inspection, MFLEX delivers quality outcomes on leading-edge flex and rigid-flex PCB technologies.
FCT, located in Minnesota USA, provides design, prototyping and volume manufacturing of flex circuits and rigid-flex boards for medical, aerospace, industrial, and IT applications.
FCT supports rigid-flex designs from prototyping to high volume manufacturing leveraging their optimized processes for quality and reliability.
Located in California, Compass Electronics provides quickturn prototyping along with low to medium volume production of rigid, flex, and rigid-flex designs. They specialize in advanced technologies including multilayer rigid-flex.
Compass uses their engineering expertise in rigid-flex PCB technology to fabricate robust designs optimized for reliability and performance. Their ITAR registration facilitates work on advanced defense and aerospace programs.
Epec manufactures printed circuits including advanced rigid, flex, and rigid-flex boards. They utilize their technical capabilities and problem solving-based engineering to produce complex multilayer rigid-flex PCBs and components.
Epec's rigid-flex expertise includes:
Epec leverages materials science, mechanical engineering, and manufacturing principles to enable innovative rigid-flex product solutions for customers.
Lenthor Engineering provides advanced PCB technologies including specialized multilayer rigid-flex boards for aerospace, defense, and medical applications. They produce high complexity rigid-flex boards certified for mission-critical functions.
Lenthor's application expertise with rigid-flex PCB technology facilitates optimizing the electrical and mechanical performance required in complex systems.
Polytech Circuits, located in Oregon, provides rigid, flex, and rigid-flex PCB manufacturing. With over 50 years of experience, they produce technologically advanced rigid-flex boards meeting demanding military, aerospace, and medical application requirements.
Polytech leverages expertise in advanced PCB technology to reliably produce leading-edge rigid-flex circuits in a highly controlled environment.
Advanced Circuits, located in Colorado, is an ITAR-certified PCB manufacturer specializing in advanced multilayer, HDI, and rigid-flex PCB production. They combine an extensive rigid PCB capability with rigid-flex technology producing complex designs.
Advanced Circuits provides an uncommon blend of advanced rigid PCB and rigid-flex technologies enabling sophisticated designs seamlessly under one roof.
Summit Interconnect provides design, fabrication and assembly services for high-complexity rigid, flex, and rigid-flex circuits. They produce reliable, high-performance PCBs spanning commercial, medical, defense, and industrial applications.
Summit Interconnect provides seamless design through manufacturing services to deliver advanced rigid-flex PCB solutions.
Here are major trends and applications fueling growth in rigid-flex PCBs:
The unique combination of characteristics make rigid-flex PCBs a top choice when density, reliability, and flexibility are required.
Compared to rigid boards and flex/flex assemblies, rigid-flex PCBs provide a range of benefits:
These characteristics make rigid-flex PCBs ideal for products requiring miniaturization, movement, and reliability.
Here is a brief comparison between key differences in rigid, flex, and rigid-flex PCB technologies:
Rigid-flex PCBs require special design and manufacturing considerations compared to all rigid or all flex boards. Here is a brief overview:
Design Complexity Rigid-flex combines electrical connectivity design with challenging mechanical engineering. Dynamic folding and static sections require extensive modeling to prevent failures.
Layer Stack Planning Integrating rigid and flex materials in one stackup requires planning insulation layers and managing thermomechanical stress.
Routing Complexity Escape routing on flex-to-rigid transitions requires expertise to avoid impedance discontinuities and signal integrity issues.
Part Sourcing Procuring compatible rigid and flex materials from the same supplier eliminates potential compatibility issues.
Fabrication Intensive Numerous lamination, drilling, imaging, and routing steps with tight process controls are needed for high yields.
Assembly Challenges Dealing with components on both rigid and flex sides, thickness differences, and warpage requires skill.
Testing Difficulties Probe and fixture access to flex areas can be problematic. Creative ICT and flying probe testing solutions help.
The combination of materials, stackups, features, and assembly make rigid-flex PCB manufacturing very challenging. Finding an expert partner is key to a successful program.
As electronic devices trend toward lighter, thinner, and more dynamic designs, rigid-flex PCB demand grows. This overview of the top 10 rigid flex PCB manufacturers worldwide highlights leaders with proven expertise capable of reliably producing high complexity multilayer rigid-flex boards. When selecting a rigid-flex partner, consider their specific experience with required layer counts, density, flex-rigid integration, and assembly processes to choose the right match. Teaming with an established rigid-flex expert provides the best path to overcoming technology hurdles and ensuring program success.
Reputable manufacturers should have certifications including:
These demonstrate disciplined quality systems and expertise.
Yes, capable manufacturers can provide fast rigid-flex prototypes within 5-7 days from design files by leveraging design for manufacturing expertise. Quick-turn prototypes facilitate proof of concept and design validation.
Providing comprehensive design data enables manufacturers to most efficiently assess and build prototypes.
Some top failure modes are:
Upfront design analysis and risk mitigation helps avoid these rigid-flex failure points.
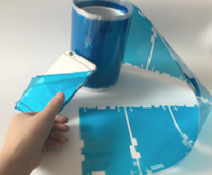
Prism Film © 2023 Benzinga.com. Benzinga does not provide investment advice. All rights reserved.