Sizing formulations are a blend of several chemicals, typically, but not necessarily, diluted in water. Sizing is used by fiber producers to “size” or coat their fibers. Sizing chemistry plays a major role in a composite’s mechanical properties such as tensile strength, fatigue resistance, and impact resistance. As well as its chemical and material properties such as hydrolysis, corrosion, oil and heat resistance. All fiber producers design their own sizing know-how and apply it to the fiber to perfectly match the requirements of the targeted applications.
Sizings consist of one or more films, forming polymeric components in dispersed, emulsified or dissolved form, as well as a lubricant, coupling agent and a range of additives such as rheology modifiers, antifoams, adhesion promoter, plasticizers, anti-static agents and surfactants. Pe Wax With Msds
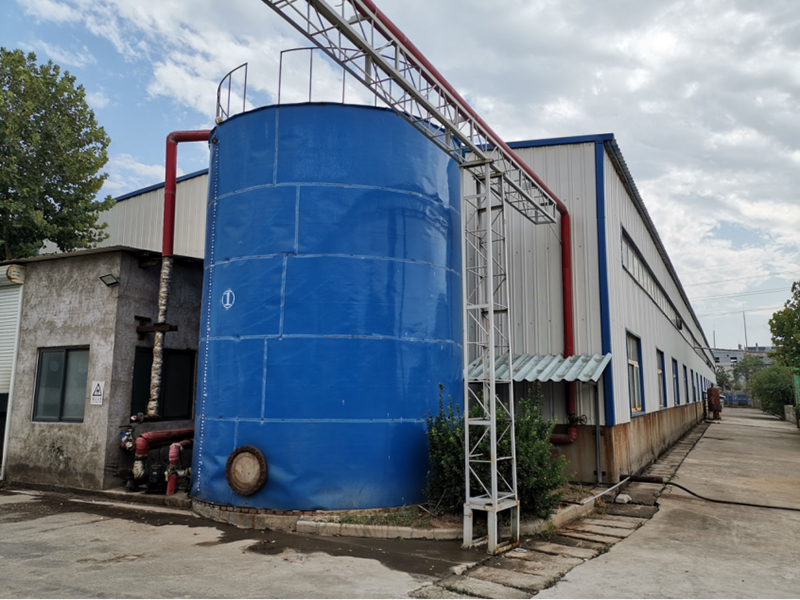
With Hydrosize® Optimized Adhesion
Without Hydrosize® Inferior Adhesion
Hydrosize® used for Glass Fiber Sizing
In the usual glass fiber sizing formulation, the film former makes up more than 70% of a sizing recipe based on solids content, and has to be stable in the final sizing formulation. It should then enhance the manufacturability of the fiber. Each contact point serves as a potential fiber break point when the fiber is being manufactured. Since these contact points are intrinsic to the process, the film former is able to protect the fiber from damage, thereby enabling maximum process efficiency. On the surface of the fiber, the film former plays a significant role in determining the properties of the final composite, such as better adhesion between the matrix and the fiber, thermal stability, mechanical properties, and water or chemical resistance.
Michelman has developed a range of lubricants, binders and film formers that are exclusively formulated for the fiber manufacturing process that deal with the unique challenges faced by the industry. The company provides solutions for specialty fibers, natural fiber, carbon fiber and fiberglass in continuous or chopped form.
Hydrosize® used for Carbon Fiber Sizing
If improving processability of the treated fiber is the only function of sizing, then it would be possible for one sizing to “fit all”. However, production and processing of the fiber are ultimately affected by sizing, which has a considerable effect on the interface properties between the composite matrix and fiber surface. The “right” sizing must make the matrix and fiber compatible. This can be largely achieved by controlling the surface chemistry of the sized fiber. Composites are rapidly changing the way we generate energy, transport goods, drive and more commonly, how industry handles problems that involve a maximum strength/minimal weight contradiction, usually with a regulatory factor. In composite manufacturing, sizing plays a complex and critical role. Michelman has the sizing formulation expertise and knowledge of end-use applications required to deal with all customer’s fiber sizing demands.
Michelman’s Hydrosize® line of products consists of sizing solutions that are specifically developed for use in the manufacturing of natural fiber, carbon fiber and glass fiber employing continuous strand or chopped strand fiberglass. These in turn are used to manufacture composite components and products.
Composite materials have structural properties that are derived mainly from fiber reinforcement. In a composite, the fiber contributes high tensile strength, improving properties in the final component, such as stiffness and strength while reducing weight. Many different types of fibers are available to reinforce polymer matrix composites. Carbon fibers and glass fibers (E-glass, S-Glass,etc.) are the most common ones. As with the matrix, the end application will determine the fiber to be selected.
Dispersions of low MW PP-g-MA (maleic anhydride grafted polypropylene) copolymers were the first sizings for polypropylene reinforcement. These dispersions were comparatively easier to make, and showed good compatibility with both the PP-g-MA coupling agents and PP matrix used in PP compounds. In recent years, fiberglass Producers tend to choose the highest molecular weight feasible, particularly for chopped strands. Generally, the higher the molecular weight of the PP-g-MA copolymer, the better mechanical properties can be attained. Michelman has also developed emulsions that offer exceptional hydrolysis resistance. In addition, the company offers a number of grades that have a low VOC content to accommodate the latest emission limitations requested by automotive OEMs.
A full list of products can be found on Michelman.com.
Key Characteristics of Maleated PP Dispersions.
Formulation for LFT PP Fiberglass
Formulation for Direct Chopped PP Fiberglass
Hydrosize® waterborne polyurethane dispersions from Michelman are film formers employed in sizing formulations that will be integrated into the production of PBT and polyamide composites. Aliphatic specific isocyanates have been selected by Michelman as building blocks that offer the best color and color stability possible.
Hydrosize® polyurethane dispersions can be used with polyamide and are formulated to react with the resins during compounding. Stability of these dispersions is maintained as such in the presence of silane, and many other grades and additives are available with soft segments to maximize thermal and hydrolytic stability. All Hydrosize® polyurethane dispersions are free from APE and solvents.
Michelman has the experience and range of products to solve customers’ next PA / PBT challenges.
full list of products can be found on Michelman.com
Formulation for Direct Chopped PA Fiberglass
Hydrosize® Link is a family of polyurethane film formers that are exclusively developed to provide increased reactivity with polyamide resin matrix. These high performance sizings are introduced during the process of fiber manufacturing and activated during compounding. Hydrosize® Link products are testaments to Michelman’s dedicated focus on the development and manufacturing of specialized polyurethane sized fiber that enhances the performance of composites in applications where materials are exposed to high temperature, ethylene glycol and water.
Formulation for LFT PA Fiberglass
Many composites require high temperature performance or high temperature processing for the most demanding applications. Typically, these applications require the use of high temperature PAEK, PEEK, PPS, polyimide or polyamide resin. The sizing will probably degrade during composite fabrication or during use, if no high temperature sizing is used on the fiber during the composite manufacturing process. As a result, outgassing causes microvoids and a poor interface. Both of these situations will decrease mechanical properties and thus lead to composite failure.
Polyimide-based Hydrosize® HP-1632 has been exclusively designed for high temperature applications. Its onset of degradation is greater than 500 °C and it is as thermally stable as most high performance resins.
Michelman uses a proprietary process to make high molecular weight epoxy dispersions without any solvent. The epoxy dispersions can be employed as fiber sizing for thermoplastic polyester, epoxy resins, and/or unsaturated thermoset polyester applications. They can also be applied to the fabric or the fiber prior to the part consolidation and/or pre-preg.
Michelman also manufactures an extensive range of synthetic and natural wax dispersions as well as acrylic based dispersions, which offer a variety of properties and are appropriate for synthetic fibers such as basalt, HMWPE or pararamid fibers.
For instance, paraffin and polyethylene (PE) wax emulsions provide adhesion control. Microcrystalline and paraffin wax emulsions can enhance ozone, vapor, moisture and water barrier properties and carnauba wax emulsions can be used as anti-block and slip additives.
Example Production Solution for HMWPE Synthetic Fiber
Need: Better adhesion between TPU and HMWPE fiber.
Solution: Michelman recommends Michem® Prime 5931 and Michem® Prime 2960 to enhance the interface between High Molecular Weight PE and TPU resin.
This information has been sourced, reviewed and adapted from materials provided by Michelman.
For more information on this source, please visit Michelman.
Please use one of the following formats to cite this article in your essay, paper or report:
Michelman Inc. (2020, May 06). Optimized Fiber-Polymer Interface Adhesion for Enhancing Composite Performance. AZoM. Retrieved on January 15, 2024 from https://www.azom.com/article.aspx?ArticleID=14177.
Michelman Inc. "Optimized Fiber-Polymer Interface Adhesion for Enhancing Composite Performance". AZoM. 15 January 2024. <https://www.azom.com/article.aspx?ArticleID=14177>.
Michelman Inc. "Optimized Fiber-Polymer Interface Adhesion for Enhancing Composite Performance". AZoM. https://www.azom.com/article.aspx?ArticleID=14177. (accessed January 15, 2024).
Michelman Inc. 2020. Optimized Fiber-Polymer Interface Adhesion for Enhancing Composite Performance. AZoM, viewed 15 January 2024, https://www.azom.com/article.aspx?ArticleID=14177.
Do you have a question you'd like to ask regarding this article?
AZoM.com - An AZoNetwork Site
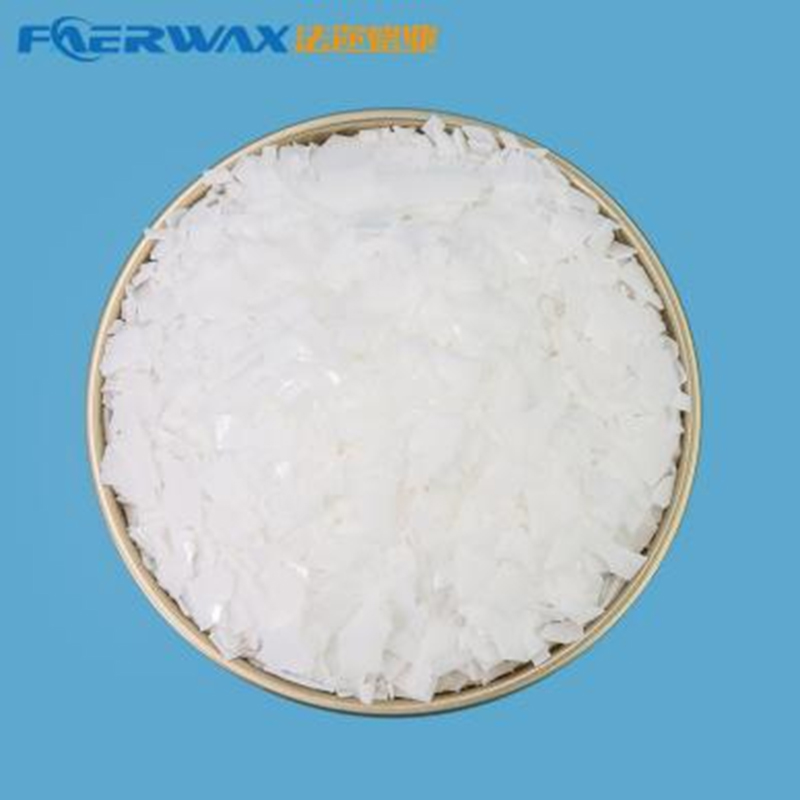
Good Coupling Graft Polypropylene Wax Owned and operated by AZoNetwork, © 2000-2024