When you think of electric motors, you usually think of magnets. But magnets are heavy, and good magnets can pose problems when you need lots of them. A technology called SESM (separately excited synchronous motors) requires no magnets, but now ZF — a German company — claims to have a different scheme using inductive excitation. Motors that employ SESM tend to be larger and require a direct current to turn the rotor. This DC is often supplied by slip rings or an AC induction with a rectifier. The innovation here is that the inductive excitation is built completely into the shaft, which the company claims makes the motor both compact and powerful.
This kind of motor is usually destined for electric vehicles. The company claims the motor reduces losses by about 15% over conventional techniques. To maximize efficiency, conventional SESM uses slip rings or brushes to transmit power to the shaft. However, ZF claims their inductive improvements are even more efficient and can reduce axial size by around 90 mm. Dct Magnet
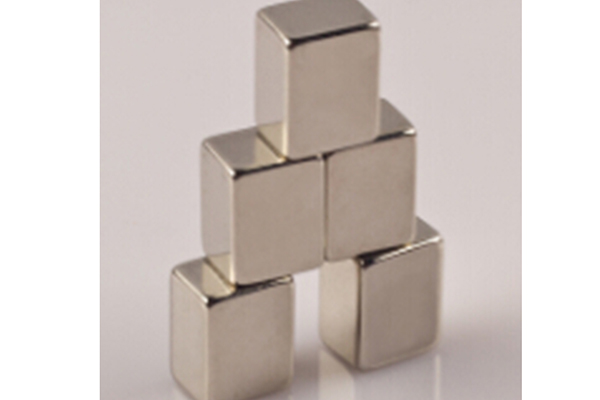
Another advantage of the technology is that there is no need to provide a dry space for slip rings. That means fewer seals and the ability to cool the rotor with oil as you would with a motor containing permanent magnets. The company plans to offer a 400 V version of the motor and an 800 V that uses silicon carbide electronics.
If you build your own motors, have you tried anything like this? Usually, we don’t see motors this big, of course. We have, however, seen builds of reluctance motors that don’t use magnets.
Cool, this would work really well for very large setups as in economies of scale such as in respect if materials versus utility Eg flywheel energy storage etc
Thats a good link in the introduction too, thanks for posting :-)
Bro, the illustration clearly shows electromagnets. 🤠🤣🤠🤣🤠 Literally all electric motors use magnets in one form or another. 😂😂😂😂😂😂😂
They don’t all use magnets (that is a fact) they do however use all use magnetism or magnetic flux such as the induction motor. For the purpose of the above it would have to be rectified as it’s AC rather than DC. Pretty interesting if you look up squirrel cage/induction motors you will see what I’ve done badly to explain! (Ps that wasn’t talking down to you 👊 my explanation /statement or lack a proper one only says yes it’s possible but betterand more technical than you can just say with words. Diagrams and current flow pictures diagrams and modelling give a way better concept Wiki will give a start if Ur interested (maybe not lol)direction
Electret and electrostatic motors do not require magnets, and when they mention voltages of several hundred, it’s clearly and electrostatic motor. They’re not used often, but were the first electric motors invented and do have interesting possibilities.
Squirrel cage motors FTW (at least in manufacturing)
Think they mean permanent magnets.
Bro, by magnets they clearly mean permanent ones, the ones made with rare earths, the expensive kind. Motors that use it constitute a Brushless Permanent Magnet Motor, or BPM.
The type of motor that uses electromagnets is a century old design called the wound rotor, which requires brushes to send DC current to the rotor to create the magnetic field.
The breakthrough that they pulled was more in regards to replacing the brushes with a new system than the rotor itself. The wound rotor is a pretty well known design.
The improvement is inductive power to excite the electromagnet, zero friction, also very clever internal oil cooling. An awesome motor.
Np, re electromagnets – the introduction covers that, wide context then dont miss stuff :-)
This 3 part series of relevance, link to part 1 first, other 2 parts linked in article
https://www.electronicdesign.com/markets/automotive/article/21270762/electronic-design-new-motor-designs-help-ev-makers-kick-the-rareearth-habit-part-1
The only photo in their press release seems to include something that looks like a slip ring. But maybe it is a high-frequency coil for the inductive transfer?
If so, seems like they’ve just replaced the 2x slip ring for DC with an AC coil and a rectifier. Nice if it works better, but somehow doesn’t seem very revolutionary.
The advantage is that in conventional designs the transformer that couples the rotor excitation current is placed in-line with the rotor and takes up extra space axially, so the motor becomes about 10 cm longer than the equivalent PM motor and the rotating transformer adds inertia. The new motor is a separately excited synchronous motor like used in industry, but it’s compressed shorter by placing the transformer inside the shaft, so it can be a drop-in replacement for a PM synchronous motor.
“the I2SM does not require any brush elements or slip rings. Furthermore, there is no longer any need to keep this area dry by means of seals.”
So it replaces the slip rings with an inductive coupling inside the shaft – how does it compare to a conventional vector controlled induction motor?
Would guess it compares to a synch motor. In manufacturing we use induction motors for anything speed controlled and synch motors for anything with like a 10:1 turndown and high torque accuracy.
TLDR: likely better for torque control
What is this clickbait title? “SPINS WITH NO MAGNETS” there has been motor without magnet for long and some don’t even have slipring or anything else… asynchronous motors exist since around 1890… This is an interesting product development but the only novel thing is how they replaced traditional sliprings with existing tech already used for other things…
A lot of innovation is refinement and always has been.
Innovation is purely the commercial exploitation of a development or invention. It doesn’t have to be groundbreaking invention with a new concept.
how is it clickbait? most innovations are refinements that often seem trivial.
It’s a little bit ckickbaity as most(?) motors contain no magnets. The squirrel-cage induction motor has been ubiquitous for over 100 years, and wound-field DC or universal motors were the norm in power tools and car starter motors until really rather recently. It was only with the development of rare-earth magnets that permanent magnet motors really took off for uses other than in childrens toys.
It is clickbait because it does use magnets… …just not permanent ones
Absolutely correct. An electromagnet is a magnet.
Want a motor without magnets? There are piezoelectric motors and a variety of electrostatic motors.
You are defo right and I corrected someone wrongly or rightly depending on how the word magnets is interpreted . That never even crossed my mind stupidly . I can’t say it’s a good way to generalise without a pre fix first, I think article was worded in such a way they knew ppl would be kicking off after that and have now started side rants lol (me that is!)
This fish does not regret eating this bait.
I have this type of motor on my junk collection still working on 250VAC 250VDC 6Amp
Also there are Synchronous Reluctance (SynRM) AC motor that basically work as a PM AC motor but without magnets. Always requires a VFD.
The neat thing about separately excited motors us that (within some reasonable range) you can adjust their kV (RPM per volt) by changing the strength of the field generated by the excitation coils on the fly and in some uses that can be the difference between needing a gearbox or not.
You can experiment with this on the cheap by taking the diode pack and regulator off a car alternator and driving the three phase legs like you would any permanent magnet synchronous motor (e.g. with a VESC in sensorless current control mode) but use a variable voltage supply to drive the excitation coil — drive it at 5v and you get high RPMs with less torqure, drive it at 10v and you get much more torque at lower RPMs. The downfall of the converted alternator is that rhe brushes that feed the field coil will wear out but it illustrates the cool things you can do with separately excited synchronous motors.
Vector control of induction motors achieves the same feat.
The VFD follows the phase angle of the induction cage by measuring the stator currents and calculates two vectors: one which corresponds to the rotor field excitation, and another that corresponds to the torque producing field 90 degrees ahead in phase. These vectors are summed up and applied to the motor. It can increase or reduce the rotor field by changing the field excitation vector.
In fact, BLDC motors are a special case of the same principle. The rotor angle is measured and the field excitation vector is known (fixed kV), so only the torque producing vector is applied.
Your first point, refering to what we call the motor constant (in S.I. units, volts / radian/ sec, equal to torque in nm/amp ) is the most important one. It means that the same top speed can be achieved with much lower battery voltage. So, for an EV with an 800V battery, it could be reduced to 400V without sacrificing low speed torque, though high speed acceleration would be halved.
Is this the paper this is all based on? https://www.mdpi.com/1996-1073/16/4/1657
There’s nothing new about synchronous motors with induction coupling to supply the rotor magnets. I’ve heard about these over a decade ago. Maybe their construction is new in that they integrated it into the shaft to make it a little more compact. But the motor still has magnets: electromagnets. The downside is that they require power to maintain their magnetic field, unlike permanent magnets. A promising alternative is a permanent magnet without rare earth elements: https://hackaday.com/2022/09/01/iron-nitrides-powerful-magnets-without-the-rare-earth-elements/
ZF are a major supplier of transmissions to the global automotive market. I guess they can see that market shrinking and want more of the EV pie. They are big enough (40 billion turnover last year) that I would tend to assume that this development is effective and worthwhile, not just some idea that is being punted out looking for funding. https://en.wikipedia.org/wiki/ZF_Friedrichshafen
Yeah, their popular 8HP (which was also licensed by Chrysler and renamed 845re and 850re) also has showed that they are used to thinking about packaging and efficiency – it’s got less losses than some of the transmissions that have more speeds, and it is made to be able to put an electric motor instead of the torque converter if you’d like to make something into a hybrid.
Also the 8HP is a conventional Torque Converter auto that shifts faster than a dual clutch, and can hold 1000+ Nm
It’s a bit less like the conventional autos normally work, imo, because it tries hard to avoid slipping the torque converter very much, preferring to downshift quickly and lock up for efficiency. It is supposed to operate (and feels like it operates) so that it is almost always locked when above a certain speed. But the fact it still has one is still nice, because when you do need to allow some slip you aren’t wearing out a clutch.
Worked for a direct competitor in this space, and often you’re already in discussions with customers early on when these types of press releases come out. That being said, I wish I was still in this space so I could get more technical info on the packaging efficiency and motivations behind this design. More power in less space was the name of the game when I left about 1 year ago basically across all types of vehicles.
Inductive excitation of synchronous machines via a rotary ransformer is nothing new. The real breakthrough here is that the primary of the transformer goes inside of the rotor and takes no additional room (if I understand it correctly, because the illustration is not very clear, I suppose it shows a disassembled motor)
While there is now an array of industrial solutions with wireless power and data (RoProxCon: 30W + GigE, SPINNER Group products, Phoenix NearFi), the earlier, the cooler the applications are:
Check out the design aspects of the Galileo orbiter: https://www2.jpl.nasa.gov/galileo/messenger/oldmess/SpinBear.html
Here’s more on the actual rotary transformer: https://coefs.charlotte.edu/mnoras/files/2013/03/Transformer-and-Inductor-Design-Handbook_Chapter_19.pdf
WoW, damn good links there helge thanks
Especially the 2nd which Ive seen chapters before circa 2004 or so by:-
COLONEL WM. T. MCLYMAN Kg Magnetics, Inc. Idyllwild, California, U.S.A.
Your JPL Nasa link certainly worth a close review, for when I have time…
As it happens I’m working on a couple of experiments related to this issue, trying to make it as minimal simple as possible but, enough for comprehensive instrumentation as I see a niggle or two worth exploring, maybe just good fun, nothing to see ;-)
Around 2003 I worked on a propellor de-icing system which used inductive power transfer to the heating elements in each propellor blade, and also serial data communications to a controller in the blades. I don’t know what happened to that system, but I see patents for similar things dated 2015. For me it marked the only time I have actually been paid for programming, in LabVIEW RealTime, of all things.
But you should know you are appreciated much more for your unpaid work even though that doesn’t put food on the table. Thank you for your service.
nonsense reverse engineering.. INDUCTION motor existed wayback centuries ago.. 😅😅😅
That configuration seems ideal for retrofit conversions
Will an car alternator do nearly the same job?
So, it uses electromagnets instead of permanent magnets. Kind of an nuanced error in the title there.
Oh, there are magnets (magnetic material), but a lot less. You have to have some ferro-magnetic material to focus, and contain the magnetic fields to make the motor more efficient.
If a motor uses a magnetic field, it has a magnet. What a nonsense clickbait title.
*Obviously* just using “magnet” as a shorthand for “permanent magnet”, which anyone reading the headline/article would understand, and it’s even specified in the article itself…
Look up piezoelectric motor designs. Marginalization of non-magnetic motors is totally something Big Magnetism would do.
And now I have to waste half a day to search back to the 20 times somebody online claimed electric cars suck because of rare earths, and I replied we’d soon have permanent-magnet-less motors, and they laughed at me, so I can laugh back at them.
Most conversations I’ve had with the anti-EVers regarding rare earth usage has been when the conversation turns to batteries. They’ll bring up the cost of over $10,000 when the battery dies and then go on to how bad environmentally the cars are because of the rare earth materials used in the batteries. Correcting them regarding their beliefs about Lithium batteries is a hit and miss often just as it is with political conversations. They’re told something they want to believe and facts hardly ever change their beliefs.
Tesla is making progress in eliminating rare earth elements in their motors – https://electrek.co/2023/03/01/tesla-is-going-back-to-ev-motors-with-no-rare-earth-elements
This is similar to a brushless alternator, which are very common in large industrial applications and also used on some motorcycles. Basically it’s just a stationary armature wound rotor alternator but with an air core transformer and rectifier instead of slip rings. You lose some efficiency but also get to eliminate a wearing part. As a motor it would have better starting and braking torque than an induction motor and possibly lower cost than a permanent magnet motor, but efficiency is still a big question.
That’s how it used to be done in the 6V automotive systems. You’ll see it a lot in old tractors, cars, and trucks.
Man this isn’t going to help bearing arcing issues at all with the current this thing induces on the shaft 😬
The article fails explain how a motor can spin without any magnetism. All electric motor need magnets, either electro-magnets or permanent magnets. It’s what causes the motion. If you claim to have designed an electric motor that dosen’t use any magnetism and is rather efficient, then explain how it works
We got these in the past, ČKD generators from about 6kW to 22kW or more, and Tatra automotive alternators.
This is normal synchronous alternator paired with small reversed alternator as exciter. The stator of the small generator is a coil that is fed DC, and the rotor are coils that make AC. This is rectified on the rotor by a diode bridge that rotates in between and the DC power is fed to the coil of the main alternator.
These guys only modified the small exciter to feed it AC, so it makes AC on the other side even when the shaft does not rotate, so the big generator can be used as a synchronous motor.
The only reason that this motor seems revolutionary to some people is that induction motors are perferred up to 10,000 Hp (7.5 MW) or so. Wound field synchronous motors are the only alternative above 30,000 Hp (22 MW). In US English, they are usually called WFSM. SESM may be a common term in other languages, but seems to be more likely invented for marketing purposes.
Induction brushless excitation has been common for wound field synchronous motors and generators for at least 25 years and more likely more than 50 years. Slip-ring WFSMs have been around for more than 100 years.
Capacitive motors and WFSMs with capacitive excitation that are suitable for industrial use have been patented, constructed and tested, Operating voltages are in the low KV range.
Here is a patent for a method of capacitive transfer of field excitation power in a wound field synchronous motor: https://image-ppubs.uspto.gov/dirsearch-public/print/downloadPdf/8736137
Please be kind and respectful to help make the comments section excellent. (Comment Policy)
This site uses Akismet to reduce spam. Learn how your comment data is processed.
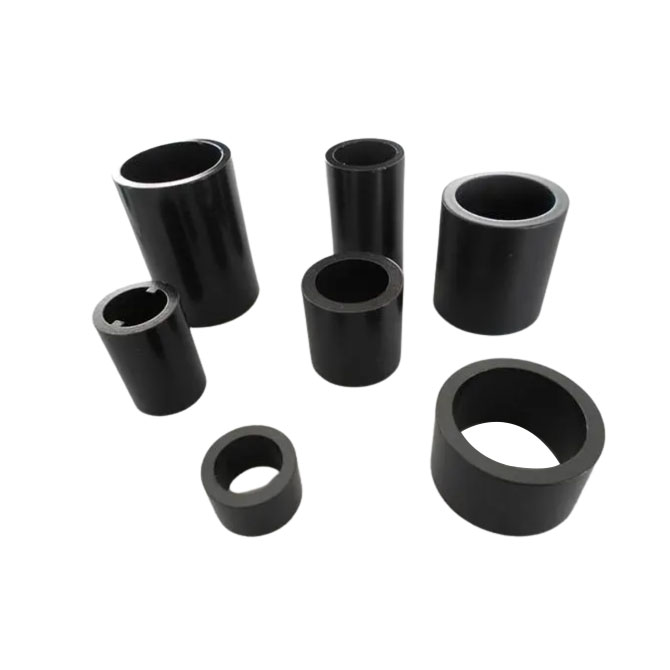
Bar Magnet By using our website and services, you expressly agree to the placement of our performance, functionality and advertising cookies. Learn more