On the “hack/not-a-hack” scale, a 3D printed bracket for aluminum extrusions is — well, a little boring. Such connectors are nothing you couldn’t buy, and even if you insisted on printing them instead, Printables and Thingiverse are full of ready-to-use designs. So why would you waste your precious time and effort rolling your own?
According to production 3D printing company [Slant 3D], a lot of times, we forget to take advantage of the special capabilities of 3D printing. The design progression of the L-bracket shown is a perfect example; it starts as a simple L, moves on to a more elaborate gusseted design, and eventually into a sturdy sold block design that would be difficult to make with injection molding thanks to shrinkage but is no problem for a 3D printer. Taking that a step further, the bracket morphs into a socketed design, taking advantage of what 3D printers can do by coming up with a part that reduces assembly time and fastener count while making a more finished, professional look. Heavy Duty Metal Hanging Brackets
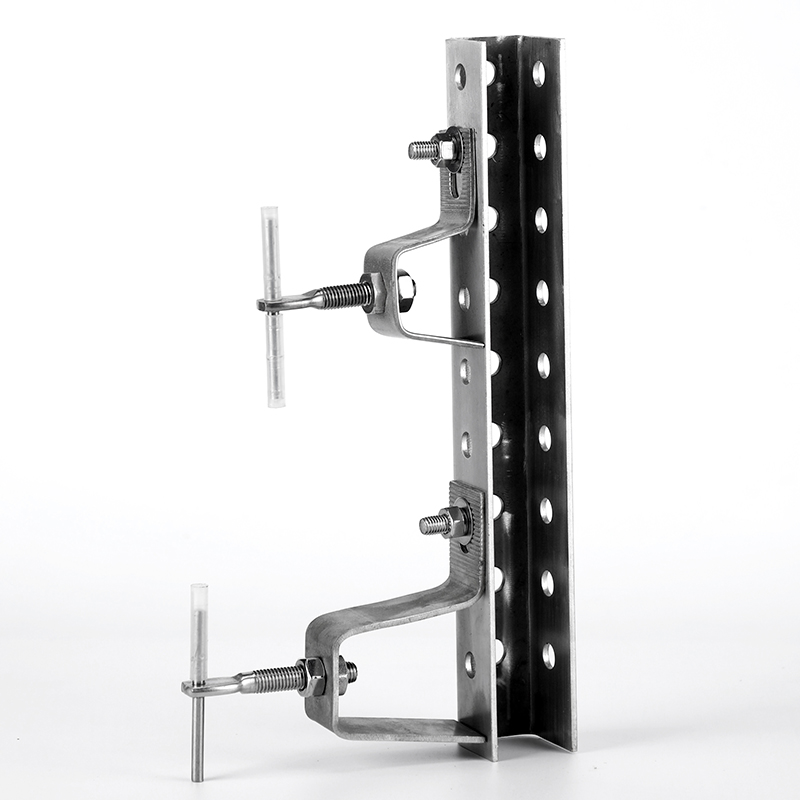
Again, this isn’t really about the bracket. Rather, it’s about a different way of thinking about your designs and leveraging the unique capabilities of 3D printers relative to other mass-production methods, like injection molding. We’ve covered some of [Slant 3D]’s high-volume design insights before, such as including living hinges and alternatives of pins and holes for assembling printed parts.
Without trying to be awkward – I think you meant ‘Solid’ and not sold in the 3rd line of the second paragraph. Thanks for the article!
HaD has had this quirk since the early days of the site. Sometimes I wonder if it’s not so much of a spelling and grammar check issue as much as an adding them in on purpose thing. Perhaps to induce extra comment traffic or for nostalgia purposes. Personally I wonder if it’s not part of some long running cryptic puzzle.
“Personally I wonder if it’s not part of some long running cryptic puzzle.”
That could explain how HaD gets its funding B^)
This could also be a way to track plagiarism as any direct copies or robo posts will pull the intentionally made mistakes. Easy to argue having the same idea, hard to argue making the same mistakes
I have a number of problems with this video. There are numerous statements like, “3d printing doesnt have to worry abotu shrinkage”, or “this part can’t be made with actual tradtional way of molding because it has so many thick areas”. An inner-wall bracket is specifically at that point of placement to limit the mechanical leverage on the part. It brings the force applied to the long arm to the OPPOSing arm along the shortest path possible. Beefing up an inner bracket is vastly supperior to encasement of a part when you want deal with the forces acting upon it.
You’re right. Shrinkage is an important factor with 3DP, whatever the material. Shrinkage has a direct impact on dimensional accuracy, tolerances, and clearances. As long as these are integrated into the design and print processes (yes, filament properties!), they’re not an issue, so one doesn’t pay attention to it anymore. Still, 99% of 3DP enthousiasts just don’t care and… have issues.
I don’t really get the popularity of this aluminum extrusion construction.
It reminds me of early RepRaps where they were all about minimizing the mass of vitamins to printed parts so they made the 3d chassis out of more-or-less 1d threaded rod. It’s like the popular science class project of making a bridge out of toothpicks and marshmallows.
So floppy, everything is a lever!!!
They say aluminum extrusion is versatile. Ok, I can see why it would be. But then, so is a sheet of MDF if you have a drill a saw and/or some sharp screws.
They say it is common and easy to obtain. Mmmm, is it? Sure, there are shops to order it at online. But in the 2020s what can’t be found online? Availability seems to come down to just cost now. And extrusion… not like buying a golden toilet but not exactly cheap either.
I really don’t get the popularity of commenting “sure that’s nice but you could do it better another way” then not providing a single link to the better solution in action. Someone does it on every HaD post.
Where’s your better mousetrap?
One huge advantage I see is that they can be used as the linear guides for motion axis, like you see on many cheap 3d printers. IDK why they insist on using the same material for the structure as well, probably just to keep it looking uniform and consistent.
As linear guides they experience wear, and it wears more in the middle on a 3d printer. Eventually it seems you have a lump in the middle of the bed, but it’s really the uneven wear on the horizontal rail.
As a real engineer who really makes things, I can promise you that aluminium structural systems are used in every single factory on this planet – because it really works! It is a super quick way of making robust tooling, with minimal design. I can give a rough sketch to a technician – I don’t have to prepare an engineering drawing – and in a couple of hours I can have something useable. The adjustability make it wonderfuly compliant – to account for tolerances – and again minimises wasted design and rework time.
I wouldn’t use a 3D printed bracket to connect the pieces, but then again, this article isn’t about the aluminium – it’s about the mechanical design process!
If some part of the assembly is 16mm too tall, you just have the too long pieces of extrusion taken out, cut to length and put back in. A far easier, cheaper, and faster process than having to rework a casting pattern, have new iron castings made, machine them, and hope nothing else will need changed.
Forget 15×15 or even 20×20 mm extrusion. Go up to the industrial size 40×40 mm and use commercially produced metal corner plates and brackets. This size of extrusion is used on mass production machinery because it’s stiff enough to withstand moving high mass at high speed. If you can pick up some surplus long pieces it’s ideal for building a 3D printer. Won’t be able to blame printing problems on frame flex with 40×40 extrusion.
Those are mad expensive and hard to obtain at times, or they come in “china metal” zinc which cracks too easily. The main issue with these “systems” is that they’re designed for the big payers in the industry who don’t mind paying ten dollars for a flat piece of steel with two holes in it, since investments are usually a tax-writeoff.
Plus the fact that nobody lists prices and everybody just makes it up as they go. If you want one bracket, that’s oh… hmm… I’ll take fifteen bucks. If you want a hundred, oh, I’ll give you 80% off because you’re such a nice guy. Unless you’re a regular customer to a trustworthy seller, you basically can’t predict what anything will cost you.
Uhmm, say what? Assuming you’re not in some third world country, aluminium extrusions and suitable fasteners should be easily available. In fact, I ordered some last Sunday and am literally building up the thing right now as the parcel provider fcked up the delivery three times in a row.
20×20 extrusion: 4.50€/meter 20×40: 7.90€/meter 40×40: 18.00€/meter 40×80: 32.10€/meter (~3.1kg/m) All extrusions are black anodized, cutting to arbitrary length is included, and you buy in increments of 0.1m (e.g. 4x 321mm 40×40 costs 23.40€ = 1.3m, they’re not rounded up per piece but per order) The heaviest size 8, M5, Item nut they had is 0.50€ a pop, 80×40 end covers are 0.70€, and the heavy 40×80 bracket sets were 6.10€ a piece. They include a cover (0.80€ individually), 4 t-nuts, 4 matching M8 screws (1.50€ if bought separately) and of course the massive bracket itself. Boring 2-screw 40×40 brackets are 1.95€ a piece (heavy) or 1.10€ (light).
Sure, that’s not free, but c’mon.
There are commercially produced 2020 brackets / plates too now. More limited quantity so cost almost as much as the 4040 ones, but they exist!
Extruded aluminum is good and you are wrong
Think knex, tinker toys or Lego that can be used to build usable structures. Attach additional things as needed. Extend it. Take it apart and reconfigure.
I like woodworking but you design it and build things and that’s it. If you want it to be something else you may attach something but usually you just start over.
Given the right set of various fittings and connectors, it’s extremely versatile and lighter and stronger than wood/mdf in most cases and looks more elegant. It’s also going to be cleaner than MDF. It allows for adjustments and modifications later too. I think you are underestimated the various fittings and parts that are out there for extrusion. Just take a look at Amazon and there are just a ton of options beyond simple right angle brackets.
Personally, I’d never 3d print fittings for this and just buy the metal ones as they are cheap and stronger.
Why use these printed right-angle brackets at all? Just use a blind joint and save the plastic.
Seriously! One quick cross-drill and you get a stronger joint for zero cost. (One screw which you were gonna use anyway.)
I understand brackets if you have to add things in the middle, or reposition them frequently, but for corners, I mean…. you know where the corners are gonna be! Cross-drill and be done with it.
It does require that your ends be cut square, but I assume anyone working with a lot of extrusion has a chop-saw with a carbide blade in it, which makes very very very quick and square cuts.
You can order pieces cut to length for smaller projects – which is why my custom 3d printer has an extrusion frame without me owning a metal saw
Interesting tidbit here is the final bracket uses aprox one width less extrusion. Not a ton mind you but because this is aimed at Mass production, would be a ton of savings for a production run of thousands of units.
It’s less then a 50 cents worth of material and higher end printers tend to use exclusively 3d printed bracket parts. Voron series is all 3d printed bracketing and is among one the best diy 3d printers you can build yourself.
Link to pins and holes goes to living hinge.
If you are using 2020 extrusions I have found it is best to not only use the corner brackets (cast aluminum, not printed) but also use waterjet cut gusset plates to support corners and junctions. Even then…the machine can still vibrate and such…but it won’t flex at the joints. This printer I made in 2014 we started with printed corner braces and gussets https://flic.kr/p/nriehV but in the end we switched entirely to waterjet cut plates and cast aluminum misumi corner braces https://flic.kr/p/nEUyz1
This machine was a variant of the Mendelmax pro (trinitylabs) which got rid of the diagonals and weak printed parts. Big Z area gains as well as stability.
I just started following this guy a bit ago – he runs a 3d print farm. About half of his videos are aimed at customers, or people that contact him looking to have something made but 3D printing can’t do what they need – and he apparently gets mad about it – so he will make a video professing that coffee cup handles should be like a rounded fin on the cup, cause that is better in every way (when in reality, it prints better, and he’s trying to sell prints). Yea, it’s really weird.
Agree! If you want a strong corner fixture in plastic, making a square hole is a very dumb idea. It’ll print fast, but as soon as there’s wear, it’ll wobble. Since he knows the profile of the aluminum bar, he could have pocketed the profile instead, meaning the whole contact surface between the plastic and the aluminum wouldn’t be 20% (for the 4 corners) but more than 80%. Much stronger, no fatigue, and also 3D printable (but it takes longer to print). Also by a physical phenomenon called buttress, no screw is even required, just a hammer.
Yes, I design all of my own 3d printed pieces that interface aluminum extrusion by sliding on such that they pocket the profile entirely. This creates not only more contact surface, but more contact surface in multiple directions that, depending on print orientation, can even stiffen the print by the shape it creates in the print.
Parts that don’t slide on can still take advantage of similar concepts.
The downside is that the design and printing involves tighter tolerances that usually require tweaks related to the specific printer and nozzle size, either in the design or in the slicing. It may also involve tweaks specific to a given manufacturer’s rail profile, even if it’s supposed to be “standard”. Equally, printing them without internal supports requires forethought in the design work, and sometimes requires some interesting design choices in terms of meeting the profile’s inner “T” extruded areas. It’s all doable, but it’s no longer “click, click, done, isn’t that pretty for YouTube!?”.
I see Slant3d content show up in recommended stuff a lot, and the titles and previews always look suspicious. George’s comment makes a lot of sense in that regard, that it’s about posturing to clients and not actually about serious mechanical engineering juxtaposed with serious ergonomic and wider system thinking design. If this article is a good representation, then really it seems like a fairly bogus/snake oil channel that’s more focused on flim flam hand waving for selling than on honesty.
For one thing, nothing makes what the video is promoting any more difficult to injection mold than anything else, other than requiring a multipart mold as designed. The shrinkage mentioned is… not even worth bringing up in context of doing professional part design. You take your material data sheet and can just apply it as a scalar to the design even. These are all knowns when designing and ordering from any even halfway reputable injection molding manufacturer. Other things require more specific work done during the design for better release/etc… but 3d printing is no different in requiring comparable specific design consideration to do well, versus simply passably.
For another, it’s… not that good of a design, even “just for demonstrating a point”. It looks nice (I guess? *as she shrugs*), and that’s about it. But it’s like it was designed by someone who never actually builds anything with aluminum extrusion (equally, I’d question whether the outer angles are the best choice, mechanically, especially over other options 3d printing/design makes readily available… not to mention all the simply flat outer walls 90 degrees to the loading). Those cast metal inner corner braces with screws and those side corner plate fixtures that the video is apparently trying to talk down? They provide room for cut tolerances (including less than perfectly square cuts) and the ability to easily see that you’ve securely gotten your pieces flush, and easily inspect for slippage during use. This doesn’t. Now, a pair of windows would solve part of that (and a good demonstration of how easy it is to iteratively prototype for realizing more problem space aspects). But… you’re still losing easy adjustability by comparison. Even before getting to other issues.
Personally speaking, I don’t 3d print parts for aluminum extrusion when there are off the shelf parts readily available that do the appropriate task properly: it’s a waste of time, money, printer time, effort, and often there are going to be hidden aspects in terms of usability or mechanics.
Which isn’t to say I don’t design and print for 3d extrusion interfacing. Highly custom, specific parts or interfaces designed as integral to a different component (ideally in ways that still involve bracketing for securing assembly rather than having to slide something all the way down a rail).
I try to focus on things where I need a custom designed piece because what is already out there won’t work well or fit well for a specific need, and working around that to use off the shelf parts anyway will require as much or more time and effort as designing something custom. Or, admittedly, things where I want a certain aesthetic and am willing to make trade offs to get it, and I have a 3d printer to do it with rather than other possible processes. Or small batch cost savings when spending the time is cheaper than ordering an otherwise expensive part (and often this turns out to have been a mistake if looking at it from a financial perspective on the time spent, lol, but it at least hones skills).
Survivorship of design is always a fascinating concept, because often there are far more aspects involved than immediately apparent. Designs that survive aren’t necessarily even the best design for the emblematic/prototypical person using them. They’re almost certainly not necessarily the best design for **everyone** or **every** use, even in the simplest of iron triangle concepts. There’s a network of concerns that includes frictions between supply side ones and demand side ones, and certain priorities of certain parties will win out even over the needs of others. Practicality. But often, designs that win out do so for multiple reasons, and just jumping past to “well I can make a thing, so why don’t I?” when something already exists in the same utility space isn’t necessarily smart, particularly as a use of time and especially energy. Sometimes it’s a big opportunity to a shortcut to success (or savings on something “adequate” for a lower tolerance purpose than what’s commonly available, or vice versa) when a new process lets you better meet even just niche demand that wasn’t being served well by the generic pre-existing part(s). But sometimes there are aspects you’re not considering… and if that’s the case, is whatever you’re working on something you care about enough to expend yourself that much on? Will you even achieve your goals, or have you embarked on a dead end quest that’s not going to have been worth the time if your only measure of worth would be financial or even commercial success (and let’s not get into how deeply commercial success relies in things that have nothing to do with how a product is designed or works compared to other available products)? What do you WANT to be spending time and focus on, and why?
I’m not trying to curb anyone’s enthusiasm: go forth and make things! All the things! But… as much as the video apparently claims to be about thinking, it’s kind of doing the opposite itself (at least judging by the article). So go forth and make things, but don’t be like that about it. Don’t be full of hubris: be the student of the world who admits they don’t know everything and is eager to learn more from everything already in existence around them, including from perspectives beyond solely their own, admitting fully that their own will always be limited and therefore miss things. Don’t assume you’re solving everyone’s problem by what solves your concept of your own. Be proud of what you make, but stay grounded and inquisitive and empathetic. Don’t convince yourself that just because you have a tool or process at hand, you have to posture like it’s the best tool for every job with pretzeled attempts at arguments to shoot down alternatives rather than simply affirm the pros of your own. Instead, learn about and learn from the strengths and modalities and processes of other things and other methods, even ones you don’t personally have the capacity for or desire to use: often the reason certain things work or are done certain ways can be deeply insightful to re-applying concepts in other domains (even knowing pottery can be useful for fdm 3d printing mechanical design work, for example, and for understanding why certain things often made in ceramic have certain design features commonly, and potential insight into related skeuomorphic vs actual usability carry over). You don’t have to try to talk down everything else to talk up your own work, if you actually understand what it’s good for and why-so in a wider context than just trying to p hack your way to claiming supremacy and success.
3 axis fdm 3d printing is, overall, a manufacturing process with a number of limits and caveats. But it’s so incredibly accessible for achieving refined results compared to “traditional” large scale manufacturing processes, also without requiring the depth of talent/training/practice/workspace and tool access needed to do more individual scale traditional manufacturing things like sculpt and cast mold blanks by hand (especially accurately) or smith metal, and most significantly allows for easy editing and iterative design compared to non digital processes. It’s so incredibly fast to having a prototype or even a working part in hand, especially with practice. It’s not the best for everything. But it’s an amazing place to get started making physical things, and it does shine in areas even beyond that context.
Your comments are probably the best thing I have ever read on Hackaday. It’s a shame the vast majority of articles don’t come anywhere close to your knowledge and humor. (Are you paying attention HD? Kaitlyn’s comments above are pure gold!)
Your second to the last paragraph is sage advice for every HD reader. Thank you and bravo!
I question any Youtube video or article that claims their thing is the “ultimate” or in this case “fully optimised”.
I didn’t even watch the video. I am an unofficial engineer though my thoughts are always thinking like a professional engineer. I would never print a corner bracket just because it’s strength is ridiculously inferior to a simple aluminum corner bracket (unless you print it 2″ thick) I didn’t get into 3d printing for paperweights, I have always printed jigs, vacuum attachments, featherboards, ect. Almost anything CAN be 3d printed somehow, but not EVERYTHING should be, some things are just not worth the time or inferior strength to do it(regardless the orientation), I still sometimes buy stainless L brackets, washers, even though it could’ve been printed.
Please be kind and respectful to help make the comments section excellent. (Comment Policy)
This site uses Akismet to reduce spam. Learn how your comment data is processed.
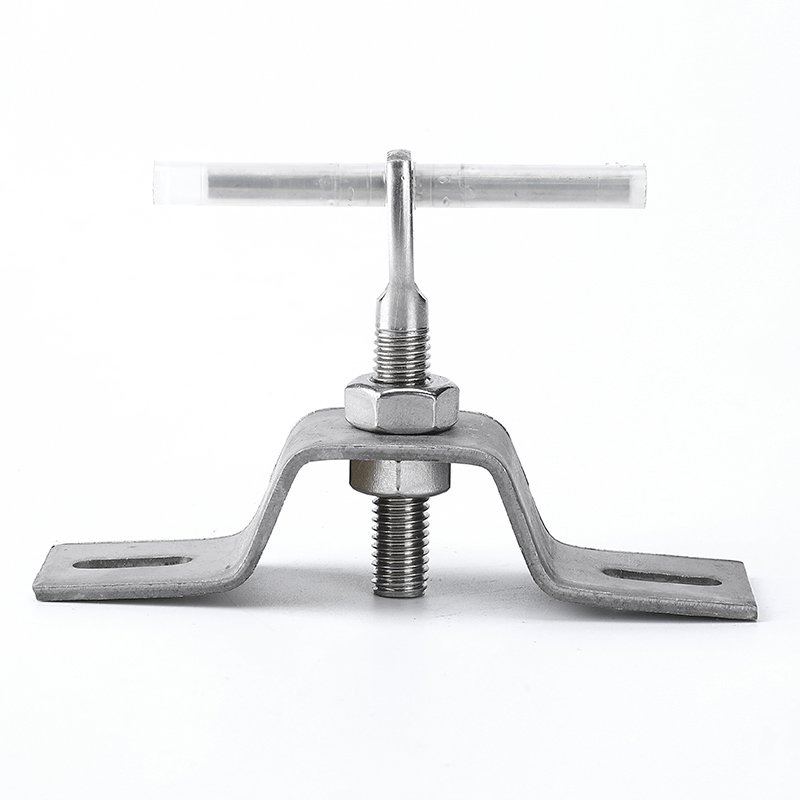
Z-Type Stainless Steel Bracket System Manufacturers By using our website and services, you expressly agree to the placement of our performance, functionality and advertising cookies. Learn more